Derived from the dual axis Blade Drive, the single axis variant has the same form factor and codebase but uses a higher power single motor power stage. This drive aims for up to 40A continuous operation at up to ~50-60V maximum supply.
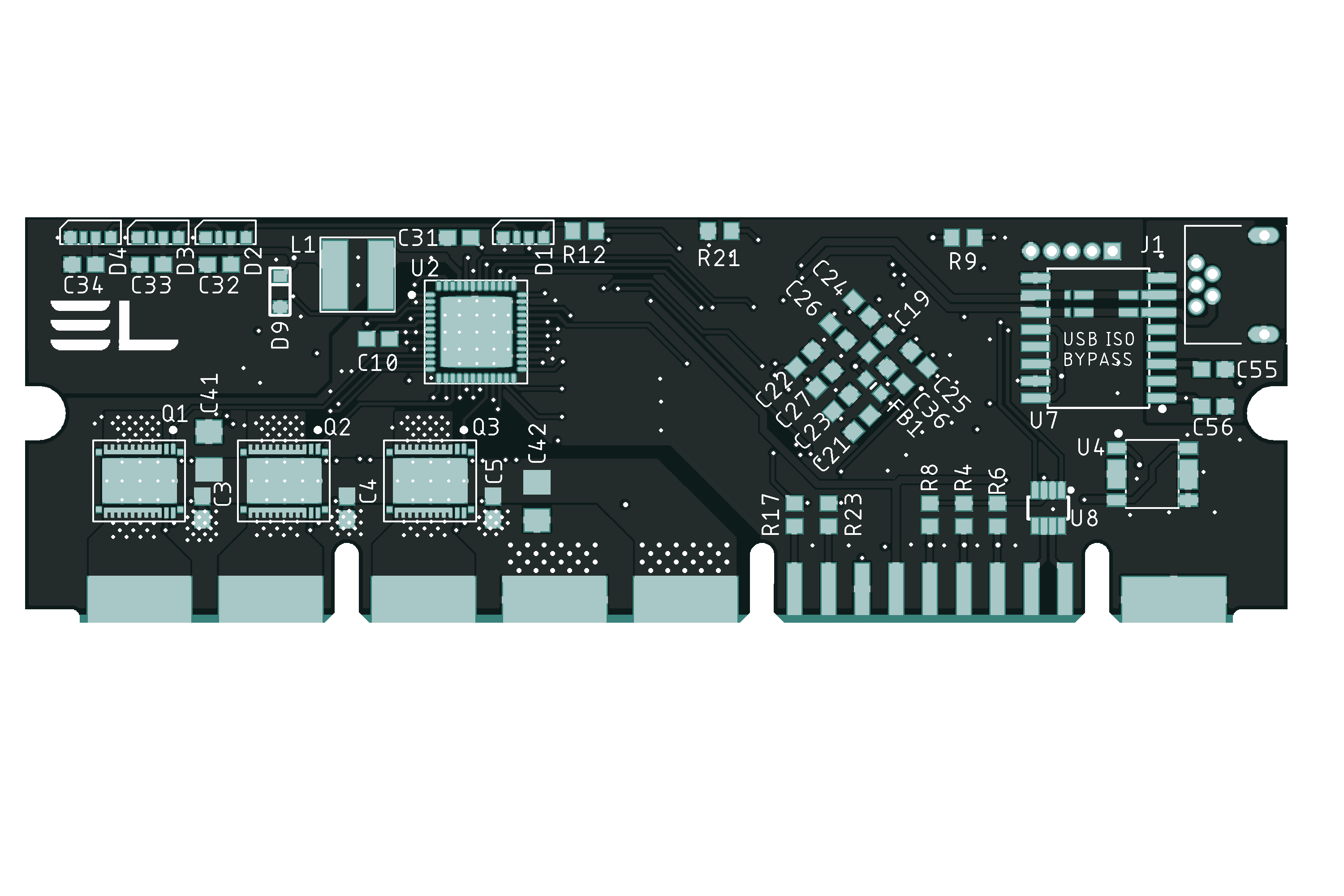
The power stage is controlled by a DRV8323RS gate driver (U2: Top Center), which has a variety of configurable gate drive parameters and fault monitoring in addition to a separate die within the IC package for a buck regulator which can be used to power the blade drive itself, or the same VDD_IN connection on the edge connector can be used to power the STM32. The mosfets controlled by the gate driver are CSD88599Q5DC (Q1, Q2, Q3: Lower Left) which are 60V 40A N channel "power blocks" which internally contain the high and low side mosfets in a single package that aims to make routing more ideal to lower impedance and improve heat dissipation. In addition to a package that has large pads for heat sinking to the PCB, these mosfets have an exposed metal surface on top to improve thermal transfer to a heat sink.
This blade drive has two new features merged in from the dual axis Blade Drive. Specifically, a CAN transceiver and the USB Isolator ICs.
The CAN transceiver TCAN330D (U8: Lower Right) adds support for communicating on a CAN (Controller Area Network) Bus to control the blade drive through a more robust electrical protocol. The firmware development to support CAN is a work in progress as of writing this post, but CAN message IDs have been started to be assigned for what various items we want to expose to the CAN bus. The current work in progress documentation for CAN ID assignment can be found here.
Additionally, the USB Isolator ISOUSB111 (U7: Top Right) was added to isolate the USB from the power ground of the blade drive, and as USB is not intended to be used there are dual solder pads to bypass the USB Isolation IC (either due to cost or availability of the IC vs the need of the feature).
Assembly and test of the board is delayed currently due to IC availability, though the firmware is ready to begin debugging the integration with the new DRV8323 once the board can be fully assembled.
For other applications, once the single axis board is working; the PCB layout could potentially be redone in order to fit into a more "typical" ESC footprint and used with the same, or higher power mosfets for applications like combat robots' drive systems.